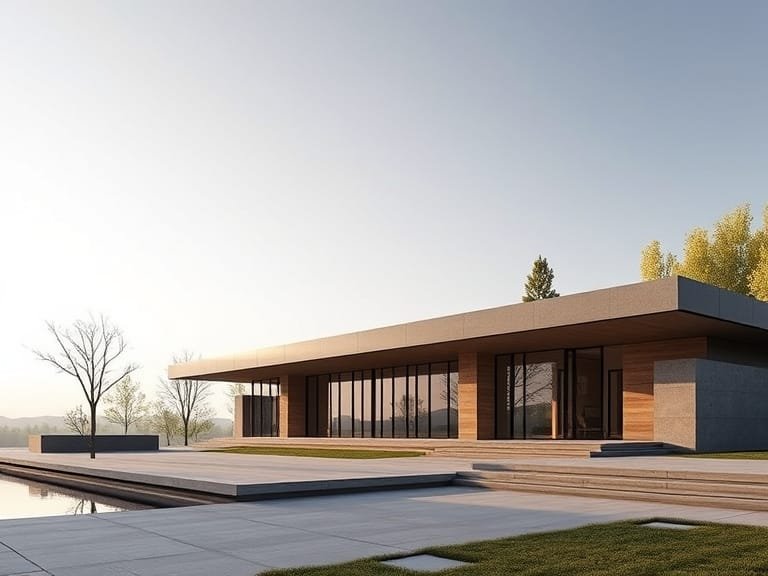
A low slope roof is defined by its gentle incline, typically characterized by a roof slope of less than 3:12. This means that for every 12 horizontal inches, the roof rises less than 3 inches. Unlike steep slope roofs, which exhibit significant vertical rise and are often used in residential settings, low slope roofs feature a more gradual incline, leading to distinct design considerations and applications in modern construction.
One of the primary distinguishing characteristics of low slope roofs is their design, which accommodates materials and systems that facilitate water drainage despite the limited pitch. This feature is crucial, as low slope roofs are susceptible to ponding water if not adequately addressed, prompting reliance on specific roofing materials that can withstand prolonged moisture exposure. Additionally, low slope roofs often employ various membranes, such as single-ply and built-up roofing systems, which are engineered to manage water effectively. These membranes are designed to be durable and resistant to the elements, ensuring longevity and functionality.
Common types of low slope roofs include flat roofs and those with slight pitches, making them especially prevalent in commercial building applications. Flat roofs, although labeled “flat,” typically have a slight grade to facilitate proper drainage. This design is widely embraced in commercial properties, including warehouses and retail spaces, due to its space-efficient advantage, allowing for rooftop installations of HVAC systems, green roofs, or solar panels. Similarly, slight pitch roofs provide subtle angles that assist in water drainage while maintaining aesthetic and architectural considerations in building design.
Given their practicality and versatility, low slope roofs are a popular choice in the construction of commercial buildings, making them a significant aspect of contemporary architecture. Their design considerations, combined with suitable applications of advanced roofing materials, ensure that they meet both functional and aesthetic requirements in today’s built environment.
Benefits of Low Slope Roof Systems
Low slope roof systems offer numerous advantages that make them increasingly popular among builders, architects, and property owners. First and foremost, one of the most significant benefits is cost-effectiveness. These roofing systems generally require fewer materials and less labor time during installation compared to their steep-slope counterparts. This can lead to lower upfront costs, which is especially appealing for commercial buildings with large roof areas.
Furthermore, low slope roofs provide excellent design flexibility. Architects can creatively utilize these roofing systems in various building designs, allowing for innovative structures that meet modern aesthetic preferences while also adhering to building codes. Their flat or gently sloping surfaces facilitate the integration of mechanical systems, including HVAC units, allowing for streamlined installation and maintenance efforts. This reduces the need for extensive structural alterations, ultimately simplifying the construction process.
In terms of energy efficiency, low slope roofs can enhance a building’s performance by accommodating roofing materials designed to reflect sunlight and reduce heat absorption. This characteristic contributes to lower energy costs, as heating and cooling demands are minimized. Additionally, the expansive surface of low slope roofs provides an exceptional opportunity for utilizing rooftop space for various functions. Property owners can install green roofs, which improve insulation and promote biodiversity, or set up recreational areas allowing outdoor activities in urban settings.
Moreover, these roof systems often require less maintenance due to their simple design, enabling easier access for inspections and repairs. Aesthetic versatility is another noteworthy advantage; low slope roofs can seamlessly incorporate a variety of materials and finishes, enhancing the overall visual appeal of the structure. Collectively, these benefits position low slope roof systems as a practical choice for a wide range of building applications, balancing performance, cost-efficiency, and visual design.
Types of Low Slope Roof Systems
Low slope roof systems are characterized by a pitch of less than 3 inches per foot. These roofs are popular in both commercial and residential applications due to their practicality, cost-effectiveness, and design versatility. Various types of low slope roofing systems include built-up roofs (BUR), modified bitumen roofs, single-ply membranes such as TPO, PVC, and EPDM, and metal roofing, each offering unique attributes and methods of installation.
Built-up roofs (BUR) are composed of multiple layers of bitumen and fabric, creating a durable and effective waterproof barrier. The installation process typically involves alternating layers of hot asphalt or coal tar, allowing for a robust and long-lasting roofing system. BUR systems are known for their excellent resistance to weather conditions, including UV rays and harsh temperatures, making them suitable for a variety of climates.
Modified bitumen roofs incorporate asphalt and modifiers to improve flexibility and performance. This roofing type is available in both peel-and-stick and torched-down application methods, allowing for adaptability to different installation preferences. Modified bitumen roofs are highly resilient and can withstand extreme weather conditions, making them ideal for both commercial and industrial buildings.
Single-ply membranes are gaining popularity due to their lightweight profile and ease of installation. TPO (thermoplastic olefin) and PVC (polyvinyl chloride) membranes are renowned for their thermal efficiency and resistance to environmental factors. EPDM (ethylene propylene diene monomer) is a synthetic rubber roofing solution known for its durability and low maintenance requirements. Each membrane type varies slightly in installation methods; however, they generally feature adhesive or mechanical fastening techniques that enhance their performance over time.
Lastly, metal roofing offers a long lifespan, typically exceeding 50 years, and is available in various materials, including steel, aluminum, and copper. Metal roofs are installed in panels or sheets and can be an energy-efficient option thanks to their reflective properties. Their resistance to severe weather conditions makes them particularly suitable for areas prone to heavy snow or rain.
Materials Used in Low Slope Roofing
Low slope roofing systems incorporate a variety of materials, each with distinct properties, performance characteristics, and aesthetic options. Understanding the main types of materials available assists property owners in making informed decisions based on their specific needs and conditions.
Asphalt is one of the most commonly used materials in low slope roofs, typically available in the form of modified bitumen. This roofing option provides durability and cost-effectiveness, making it a popular choice for many commercial and residential properties. The composition of modified bitumen includes a blend of asphalt and polymer, which enhances flexibility and resistance to temperature fluctuations and UV rays. Its installation can be achieved through torch-applied or adhesive methods.
Another frequently utilized material is rubber, specifically in the form of Ethylene Propylene Diene Monomer (EPDM). This single-ply membrane has gained popularity due to its excellent waterproofing capabilities and resistance to harsh weather conditions. EPDM roofs are lightweight, easy to install, and provide a long lifespan. Additionally, they require minimal maintenance, making them an appealing option for cost-conscious property owners.
Thermoplastic polyolefin (TPO) and polyvinyl chloride (PVC) are notable thermoplastic options praised for their energy efficiency and heat reflectivity, which can contribute to lower energy costs. Both materials are available in large sheets that can be mechanically fastened or adhered to the roof deck. TPO is known for its ability to withstand UV radiation and chemical exposure, while PVC is more puncture-resistant and often considered an ideal choice for roofs with high-temperature applications.
Lastly, metal roofing is another viable option, renowned for its longevity and resistance to elements. Materials such as galvanized steel, aluminum, and copper provide exceptional durability and can also be sourced in various finishes for enhanced aesthetics. Metal roofs are lightweight and recyclable, making them an environmentally friendly alternative.
In selecting the appropriate materials for low slope roofing, readers should consider factors such as budget, local climate conditions, durability, and aesthetic preferences. Each material’s unique attributes can affect long-term performance, necessitating thorough evaluation to ensure the best choice for specific roofing needs.
Installation Techniques and Best Practices
Installing a low slope roof requires careful consideration and adherence to established techniques to ensure its effectiveness and longevity. First and foremost, it is essential to follow the manufacturer’s guidelines for the specific roofing system being utilized. These guidelines provide crucial details that influence installation, including the materials required, fastening methods, and specific environmental conditions to consider.
Preparation is a critical step in the installation process. This entails ensuring that the roof deck is clean, dry, and properly inspected for any damages before the application of roofing materials. Any imperfections should be addressed to create a smooth surface for installation. Additionally, maintaining a proper drainage plan is vital. A well-designed low slope roof should facilitate water drainage effectively to prevent pooling, which may lead to premature roofing failure. Installing tapered insulation or crickets can help achieve the desired drainage slope without needing to alter the roof structure significantly.
Insulation is another important consideration. Using high-quality insulation not only enhances thermal performance but also contributes to the overall energy efficiency of the building. When selecting insulation, it is crucial to ensure that it conforms to local building codes and the manufacturer’s recommendations. The sealing process is equally significant; using appropriate sealants and adhesives can prevent leaks and enhance waterproofing capabilities. A systematic approach to sealing joints, seams, and penetrations further aids in creating a robust low slope roofing system.
Finally, selecting qualified contractors ensures that the installation adheres to industry standards. It is worthwhile to check for credentials, reviews, and past projects before making a decision. Engaging professionals with experience in low slope roofing will greatly reduce the risk of costly mistakes. Establishing a proper installation schedule is also fundamental in coordinating the various aspects of the project, minimizing downtime, and ensuring that all work is completed efficiently.
Common Issues and Maintenance for Low Slope Roofs
Low slope roof systems, while advantageous in certain architectural designs, are notably susceptible to specific issues that can compromise their longevity and functionality. One of the most prevalent problems encountered is ponding water. When water accumulates on the roof surface and does not drain efficiently, it can lead to membrane deterioration and ultimately result in leaks. This stagnation not only poses a risk of structural damage but can also create conditions favorable for mold and mildew growth, further aggravating maintenance concerns.
Leaks are another significant issue associated with low slope roofs. Determining the origin of a leak can sometimes be challenging due to the flat nature of the roof. Regular inspections, ideally conducted biannually or after severe weather events, are crucial in identifying potential leak sources. Signs such as water stains on the ceiling, dampness on the walls, or unexplained moisture in the insulation warrant immediate attention and possible repairs.
Moreover, the roofing membrane can deteriorate over time due to UV exposure, temperature fluctuations, and other environmental factors. This deterioration can lead to cracks, punctures, and even complete membrane failure if not addressed promptly. Therefore, a preventative maintenance plan is essential for extending the lifespan of low slope roofs.
To mitigate these issues, implementing a comprehensive maintenance routine is recommended. Regularly scheduled inspections can help spot any early indicators of wear or damage. Keeping the roof surface clean and clear of debris is equally important, as this ensures proper drainage and minimizes the risk of water accumulation. Additionally, addressing minor repairs immediately can forestall more extensive and costly issues down the line, ultimately protecting the investment in the low slope roof system.
Building Codes and Regulations
Low slope roof systems are subject to a variety of building codes and regulations that vary at the national, state, and local levels. The compliance with these regulations is imperative not only to ensure safety but also to promote sustainability and mitigate potential insurance liabilities. Nationally, the International Building Code (IBC) serves as a primary framework that regulates structural integrity, fire safety, and energy efficiency for low slope roofs. Additionally, the National Roofing Contractors Association (NRCA) offers guidelines specifically tailored to roofing practices, ensuring quality installations that meet statutory requirements.
At the state level, individual codes may be influenced by local climatic conditions and environmental standards. For example, areas prone to heavy snow loads may enforce stricter requirements to ensure roofs can effectively handle added weight. Furthermore, local jurisdictions typically adopt their regulations, which can further refine guidelines established by state codes. This layered approach promotes a safer, more resilient roofing system tailored to each community’s needs.
Understanding the significance of compliance is crucial. Failure to adhere to building codes can lead to severe repercussions, including safety hazards, costly repairs, or even litigation in the event of an incident related to structural failure. Insurance companies often require proof of compliance during assessments, as non-compliance may affect coverage options or claims. Therefore, it is essential for homeowners and contractors to diligently research and adhere to all relevant codes throughout the roof planning or renovation process.
Resources such as the local building department, state regulatory agencies, and online databases can provide valuable information regarding applicable building codes. Additionally, engaging with professional roofers who are knowledgeable about current regulations can aid in ensuring that projects are compliant, safeguarding both the property and its occupants.
Cost Considerations for Low Slope Roofing
When assessing low slope roofing systems, the cost implications play a pivotal role in the decision-making process. Various factors influence the overall expenses, which include material selection, installation methods, maintenance requirements, and potential lifecycle costs. Understanding these components is essential for clients as they budget for their roofing projects.
The choice of materials significantly impacts the cost of low slope roofs. Common materials include Modified Bitumen, TPO (Thermoplastic Olefin), EPDM (Ethylene Propylene Diene Monomer), and PVC (Polyvinyl Chloride). Each of these materials offers distinct advantages and costs; for instance, TPO is known for its energy efficiency, while Modified Bitumen provides enhanced durability. The pricing can vary widely based on the quality of the material, with premium options often yielding better long-term performance and reduced maintenance needs.
Installation practices also affect cost dynamics. Professional installation by experienced roofers is crucial, as improper installation can lead to costly repairs down the line. The complexity of labor required, especially for challenging roof designs or tight timelines, can inflate installation costs. On the other hand, cutting corners to minimize expenses may result in higher maintenance costs later. Therefore, clients should prioritize hiring reputable contractors to ensure quality workmanship.
Maintenance is another cost consideration that can be overlooked initially but is essential in budgeting for low slope roofing systems. Regular inspections and maintenance can prolong the roof’s lifespan, reducing the frequency of major repairs or replacements. Additionally, potential lifecycle costs should be evaluated; a roof with a longer lifespan and lower maintenance requirement may prove more economical over time, despite higher upfront costs.
Clients might also explore financing options available for roofing projects, including loans or leases, to better manage upfront expenditures. Furthermore, evaluating the return on investment (ROI) of different roofing systems can provide insight into choosing a solution that aligns with both budgetary constraints and long-term strategic goals.
The Future of Low Slope Roofing
As the demand for sustainable building practices continues to grow, low slope roofing systems are evolving to meet contemporary environmental challenges and efficiency standards. One of the most prominent trends is the incorporation of eco-friendly materials in roofing solutions. Manufacturers are increasingly focusing on materials that are not only durable but also recyclable or made from recycled components, thereby reducing the overall carbon footprint of construction projects. These advancements not only contribute to a greener planet but also satisfy consumer demand for sustainability.
Energy-efficient designs are another crucial aspect of future low slope roofing. Innovative systems, such as green roofs that incorporate vegetation, help to insulate buildings while simultaneously urbanizing the environment. This design contributes to improved air quality, mitigates urban heat effects, and enhances biodiversity within cities. Similarly, the development of reflective roofing options, designed to deflect solar radiation, plays a vital role in reducing energy costs and improving indoor temperatures.
Technological advancements in both materials and installation techniques hold significant promise for the evolution of low slope roofs. For instance, the rise of advanced adhesives and seamless membrane systems not only improves waterproofing but also optimizes installation efficiency. These innovations reduce labor costs while ensuring high-quality finishes that prolong the lifespan of roofing systems. The integration of reflective coatings, which contribute to energy savings by maintaining cooler surface temperatures, reflects a shift toward more adaptable and sustainable roofing solutions.
In conclusion, the future of low slope roofing systems is poised to make substantial contributions to sustainable building practices. Through eco-friendly materials, energy-efficient designs, and significant technological advancements, low slope roofing will play a vital role in enhancing urban ecology and promoting sustainability, all while meeting the growing demands of modern architecture.