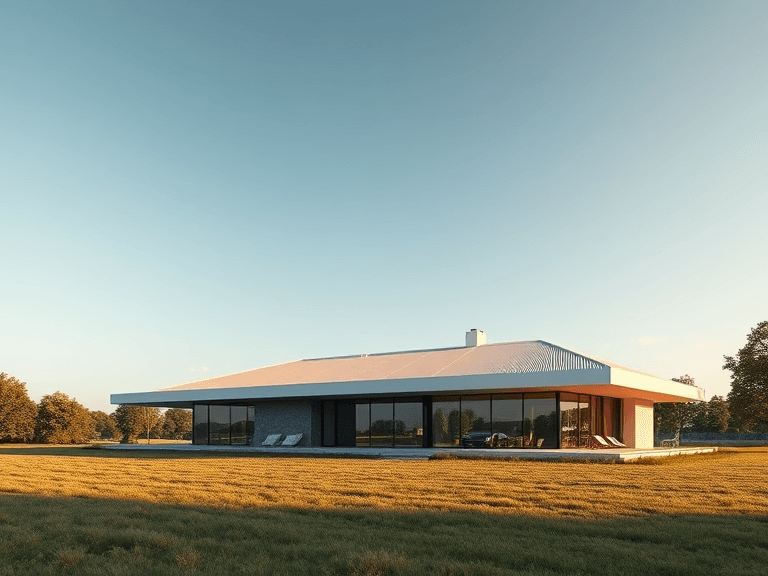
Low slope shingles represent a distinctive category of roofing materials specifically designed for roofs with a gentle pitch, commonly ranging from 2:12 to 4:12. Unlike traditional asphalt shingles that require steeper angles for effective water runoff, low slope shingles employ unique characteristics and materials to ensure adequate performance in managing water flow and drainage. These roofing solutions are particularly beneficial in urban settings, where flat or low sloped roofs are prevalent due to architectural design and space constraints.
The materials utilized in low slope shingles differ from their traditional counterparts. Often composed of modified bitumen, thermoplastic olefin (TPO), or ethylene propylene diene monomer (EPDM), these shingles are engineered to offer superior durability and resistance to harsh weather conditions. Their design not only aids in preventing leaks and water infiltration but also provides UV resistance, extending the lifespan of the roofing system.
Another significant aspect of low slope shingles is their functionality regarding aesthetics and versatility. Available in various colors and textures, low slope shingles can complement a wide array of architectural styles, enhancing the overall visual appeal of a building. Moreover, low slope roofs can accommodate additional features such as rooftop gardens, HVAC systems, and even recreational areas, making them highly functional in urban environments.
One of the primary concerns associated with low slope roofs is water drainage. Low slope shingles are artfully designed to mitigate ponding water through the incorporation of specific drainage systems and the careful installation of sloping plans. This ensures that water does not accumulate, which could lead to significant damage over time. Overall, understanding low slope shingles: a guide to their definition, properties, and applications is crucial for those considering them for residential or commercial use.
Types of Low Slope Shingles
Low slope shingles encompass a variety of roofing materials, each with unique characteristics and advantages. Among the most common types are modified bitumen, EPDM (ethylene propylene diene monomer), TPO (thermoplastic polyolefin), and built-up roofing (BUR). Understanding low slope shingles: a guide through these options reveals how they differ in composition, installation, durability, and cost-effectiveness.
Modified bitumen roofing consists of asphalt sheets that have been enhanced with modifiers for added flexibility and durability. Typically installed in a torch-down or self-adhered manner, modified bitumen offers excellent waterproofing capabilities. Its lifespan generally ranges from 10 to 20 years, and while installation costs can be moderate, the long-term maintenance requirements can influence overall expenditures.
EPDM, a synthetic rubber roofing membrane, is another popular choice for low slope applications. Known for its light weight and exceptional weather resistance, EPDM can endure extreme temperature fluctuations and UV exposure. The installation process generally involves adhesive application or mechanical fastening, leading to a lifespan of 20 to 30 years. Cost-wise, EPDM is often seen as a budget-friendly option, appealing to those seeking affordability without sacrificing durability.
TPO is increasingly gaining popularity due to its energy-efficient properties. Made from a blend of polypropylene and ethylene-propylene, TPO roofing membranes are typically installed using mechanical attachments or adhesive. This type tends to be white or reflective, enhancing energy savings in warmer climates. While TPO’s lifespan can exceed 20 years, its initial costs could be higher compared to modified bitumen, though the potential for reduced energy expenses can be a noteworthy counterpoint.
Built-up roofing (BUR), characterized by layers of asphalt and felt, has been a traditional choice for low slope roofs for decades. Known for its reliable protection, BUR systems can be quite durable and offer excellent waterproofing. However, the installation tends to be labor-intensive, contributing to higher upfront costs. Despite its longevity, maintenance and repair can become necessary over time.
In essence, each type of low slope shingles presents distinct advantages and challenges. Selecting the optimal option will depend on individual requirements, particularly regarding budget, longevity, and specific environmental conditions.
Advantages of Choosing Low Slope Shingles
Low slope shingles offer a variety of benefits, making them an attractive option for both residential and commercial properties. One of the key advantages of these shingles is their excellent waterproofing properties. Due to the unique design and installation methods, low slope shingles are particularly adept at channeling water away from the roof surface, thereby reducing the risk of leaks or water damage, which can be crucial in areas with heavy rainfall or snowfall.
Another significant benefit is the longevity associated with low slope shingles. When properly installed and maintained, these roofs can last for several decades, providing a long-term solution for those looking to invest in durable roofing options. The materials used in low slope shingles are often resistant to weather-related wear and tear, contributing to their extended lifespan.
Energy efficiency is another notable advantage of low slope shingles. These roofs can be designed with reflective coatings that help minimize heat absorption, thereby reducing energy costs for heating and cooling systems. This not only contributes to lower utility bills but also supports environmentally friendly practices, aligning with modern sustainability goals.
Low slope shingles also cater to contemporary design aesthetics, complementing various urban architectural styles. Their versatility allows for creative applications in both commercial and residential settings, making them suitable for a wide range of building designs. Whether used on flat rooftops or incorporated into sloped structures, low slope shingles can enhance the overall visual appeal of a property.
In conclusion, the advantages of low slope shingles encompass their waterproofing capabilities, durability, energy efficiency, and aesthetic flexibility. These features contribute to their growing popularity among property owners seeking reliable and stylish roofing solutions.
Challenges and Considerations with Low Slope Shingles
Low slope shingles, while offering certain aesthetic and practical advantages, present a unique set of challenges and considerations. One of the most significant issues associated with low slope roofs is potential drainage problems. Unlike steep-slope roofs that allow for a natural gravitation of water runoff, low sloped roofs are often susceptible to water pooling, especially in areas where the slope is not adequately uniform. This can lead to what is known as ponding water, which can compromise the integrity of the roof over time, ultimately causing leaks or structural damage.
The risk of ponding water is particularly acute during heavy rainfall and snowmelt periods. Homeowners should recognize that if water collects on the roof for prolonged periods, it can lead to significant wear on the shingles. This necessitates stringent care and management during such weather conditions. Moreover, the material integrity may diminish, resulting in decreased durability and longevity. Thus, understanding low slope shingles requires a proactive approach to prevent such complications.
Another consideration is the impact of weather conditions on the performance of low slope shingles. Factors such as temperature fluctuations, UV exposure, and ice accumulation can all affect the shingles’ lifespan. Therefore, homeowners should be vigilant about maintaining their roofing systems. Regular inspections can help identify issues before they escalate. Common mistakes to avoid include improper installation of the shingles, which can exacerbate drainage problems, and neglecting routine clean-ups that prevent debris accumulation.
In light of these challenges, thorough understanding and careful planning when dealing with low slope shingles are essential. A well-informed approach can enhance not only the aesthetic appeal of a home but also ensure the roof’s functionality and resilience against the elements.
Installation Process of Low Slope Shingles
When it comes to installing low slope shingles, a methodical approach is essential to ensure durability and longevity. The first step in the installation process involves thorough preparation of the application surface. This preparation includes cleaning the roof deck of debris and repairing any underlying damage, which may require replacing rotting wood or fixing leaks. Priming the surface is paramount as it provides an effective bonding surface for the shingles and adhesives, ensuring a more robust installation.
Once the surface is prepped, the next stage involves layering the shingles. The installation typically starts from the lowest point of the roof and progresses upwards. Each row of shingles should be carefully aligned to create a straight line, which is crucial for proper water drainage. Additionally, adhesive must be applied to the shingles and the deck to secure them in place. A consistent application of adhesive is necessary to ensure that the shingles adhere effectively without weakness, reducing the risk of future water penetration.
During the layering process, ensuring proper overlap between shingles is another critical aspect. An appropriate overlap helps prevent water from seeping under the shingles during storms or heavy rainfall. Typically, a three-inch overlap is recommended for optimal performance. It is also advisable to check local building codes to confirm any specific requirements regarding shingle installation. Safety measures should not be overlooked, which include wearing appropriate gear such as harnesses and non-slip shoes. Basic tools required for installation encompass a utility knife, chalk line, trowel for adhesive application, and safety equipment. By following these systematic steps, DIY enthusiasts and professionals alike can confidently navigate the process of understanding low slope shingles and achieve high-quality results that ensure the longevity of the roof.
Maintenance Tips for Low Slope Shingles
Maintaining low slope shingles is crucial for ensuring their longevity and effectiveness in protecting your home from the elements. Regular inspections should be the foundation of your maintenance routine. Visiting your roof at least twice a year, ideally in spring and fall, allows homeowners to identify any wear or damage early. During these inspections, look for signs of cracks, blisters, or areas where shingles may be lifting. Such issues, if left unattended, can lead to serious water infiltration problems.
Cleaning low slope shingles is another essential practice in their maintenance. Debris such as leaves, branches, and dirt can accumulate on the roof and inhibit proper drainage, leading to water pooling. This can significantly decrease the lifespan of your roofing material. Using a soft-bristle broom or a blower can effectively remove debris without causing damage to the shingles. Furthermore, it is advisable to clean gutters and downspouts regularly to ensure that water flows freely. This not only enhances the roof’s performance but also prevents potential water issues that may arise from clogged drainage systems.
Homeowners should also be vigilant in monitoring the condition of the shingles after severe weather events such as storms or heavy snowfall. Inspect for any signs of damage, including lifted edges or missing shingles. Addressing these issues promptly is vital for maintaining the roof’s integrity. If you discover substantial damage or feel uncertain about carrying out repairs, hiring professionals with expertise in low slope shingles can ensure that the work is done correctly. In conclusion, regular inspections, effective cleaning, and prompt repairs are critical to preserving the performance and durability of low slope shingles.
Best Practices for Repairing Low Slope Shingles
Repairing low slope shingles is an essential process that ensures the durability and longevity of roofing systems, especially in areas prone to water accumulation. To begin, it is crucial to identify any visible damage to the shingles, including curling, blistering, or missing sections. These signs often indicate underlying issues that may need immediate attention. Assessing the severity of the damage allows homeowners to decide on suitable repair solutions, whether they are minor patches or more extensive replacements.
For patching leaks in low slope shingles, the first step involves cleaning the affected area to remove any debris or dirt. Following this, a quality roofing adhesive should be applied to the shingle edges where damage is present. After adhering the patch, it is advisable to seal the edges with a roofing sealant designed for low slope applications to enhance waterproofing. Replacing damaged sections is another method of repair, which involves lifting the existing shingle and carefully removing it. Once the damaged piece is taken out, an appropriate replacement shingle can be installed, ensuring it aligns with the surrounding shingles for a seamless appearance.
Resealing edges also plays a crucial role in the maintenance of low slope shingles. Over time, the sealant may deteriorate due to exposure to elements, making it essential to inspect these areas regularly. Reapplying sealant helps to prevent leaks by creating a robust barrier against moisture infiltration. Homeowners should educate themselves about when to engage professional services versus opting for DIY repairs. Generally, if the repairs exceed the homeowner’s skill level or if extensive damage is apparent, contacting a professional is advisable to ensure all repairs are performed correctly.
Proper maintenance of low slope shingles through effective repair practices contributes significantly to the overall resilience and functionality of a roofing system, safeguarding against potential water damage.
Regulations and Building Codes for Low Slope Roofing
When undertaking a roofing project involving low slope shingles, it is crucial to understand the intricate web of regulations and building codes that govern their installation. These codes vary significantly across different local jurisdictions and at national levels, establishing guidelines that aim to ensure safety, durability, and performance. Compliance with these regulations is not just a legal obligation but also a means to secure the longevity and functionality of the roofing system.
For low slope roofing, specific standards are set by organizations such as the American National Standards Institute (ANSI) and the International Building Code (IBC). These standards dictate various elements, including material specifications, installation practices, and structural requirements. For instance, low slope shingles must be installed at specific angles to ensure proper water drainage and minimize the risk of leaks. Additionally, the choice of materials is often regulated to enhance fire resistance and weatherproofing capabilities.
In many jurisdictions, obtaining the necessary permits is a prerequisite for initiating roofing work. This typically involves submitting detailed plans for review to ensure that the proposed roofing solution aligns with local zoning laws and safety standards. Additionally, inspections may be mandatory throughout the installation process to verify adherence to the building codes. Failure to obtain proper permits or to comply with building regulations can lead to penalties, necessitating costly rework and potential legal issues.
Moreover, local building codes may also address warranty guidelines for low slope shingles to ensure homeowners receive adequate protection against defects or failures. It is essential for contractors and property owners alike to stay informed regarding the applicable regulations to avoid future complications. Understanding these aspects of low slope roofing can provide peace of mind and assurance that the installation remains compliant, safe, and durable.
Choosing the Right Contractor for Low Slope Shingles
When it comes to understanding low slope shingles, choosing the right contractor is a critical step in ensuring a successful installation or repair. The process begins with evaluating potential contractors’ qualifications, as their experience directly impacts the quality of the work. Look for contractors who specialize in low slope roofing systems, can demonstrate knowledge of the materials, and have a solid portfolio of prior projects. This specialization is essential because low slope shingles often require specific techniques that differ from traditional roofing.
Additionally, checking licenses is paramount. Each state has its own licensing requirements for contractors, and hiring a licensed professional ensures that they meet local standards. Validating proper insurance coverage is also advisable, as it protects both parties in the event of accidents or damages during the project.
Reading reviews and testimonials from previous clients can provide insights into the contractor’s reliability and work quality. Online platforms and local community boards are excellent resources to gather this information. Look for contractors with consistently positive feedback, as well as those who address negative reviews responsibly. This reflection often indicates their level of professionalism and customer service.
Obtaining multiple quotes can help you compare costs effectively, ensuring that you do not overpay for services. Be cautious of unusually low prices, as they may indicate cutting corners or inferior materials. Instead, aim for a balance between affordability and quality.
Lastly, effective communication with your chosen contractor is vital. Clearly articulate your expectations, budget, and timeline. A trustworthy contractor will be open to discussing these factors and addressing any concerns. By fostering a transparent relationship, you set the groundwork for optimal results and satisfaction in your low slope roofing project.